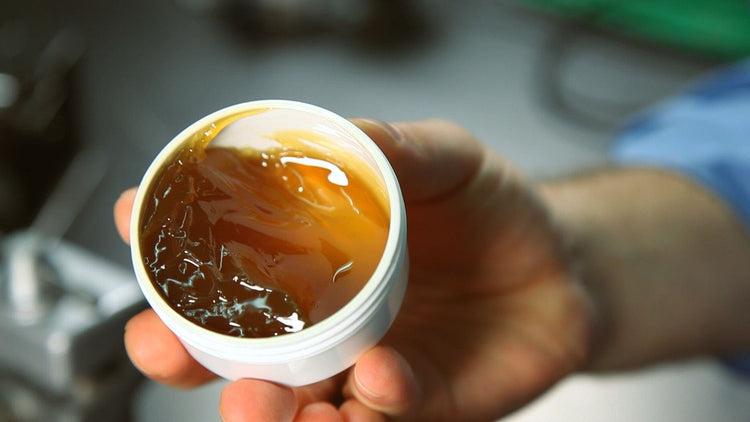
Collection: Soldering Chemicals
-
Johnson J-33 Galvanized Steel Flux - Gallon
Regular price $59.99Regular priceUnit price / per -
Johnson J-33 Galvanized Steel Flux - Quart
Regular price $19.99Regular priceUnit price / per -
Johnson No.1 Stainless Steel Flux - Gallon
Regular price $59.99Regular priceUnit price / per -
Johnson No.1 Stainless Flux - Quart
Regular price $23.99Regular priceUnit price / per -
RubyFluid Paste Flux - Soldering Flux - 1 lb Jar
Regular price $13.95Regular priceUnit price / per -
Alpha 116844-0001, NR205 No-Clean Soldering Flux, 1 Gallon Pail
Regular price $79.00Regular priceUnit price / per -
PF440 Rosin Paste Flux - 1 LB Jar
Regular price $20.98Regular priceUnit price / per -
Alpha 148691-0001, EF-6100 No-Clean Soldering Flux - 1 gallon size
Regular price $71.00Regular priceUnit price / per -
Alpha 116125-0001, 870-25 Water-Soluble Touch-Up Soldering Flux - 1 gal Pail
Regular price $141.00Regular priceUnit price / per -
Alpha Metals 115948-0001, 615 RMA Mil Flux - 1 gal pail
Regular price $75.00Regular priceUnit price / per -
Qualitek 35 Defoamer - 16 oz
Regular price $30.98Regular priceUnit price / per -
Alpha 115233-0005, 3355-11 Organo-Flux Water-Soluble Soldering Flux - 5 Gal Pail
Regular price $280.00Regular priceUnit price / per -
Qualitek 35 Defoamer - 1 Gallon Pail
Regular price $129.98Regular priceUnit price / per -
Alpha 152730-0005, EF-6103 No-Clean Wave Solder Flux - 5 Gal Pail
Regular price $423.00Regular priceUnit price / per -
Alpha 116844-PENS, NR205 No-Clean Soldering Flux Pen
Regular price $6.95Regular priceUnit price / per -
Alpha AM51055 Waterflow 2000 Paste Flux, 16 oz JAR
Regular price $24.99Regular priceUnit price / per -
Alpha 115226-0005, NF373 Neutral-Flux Water-Soluble Wave Solder Flux - 5-gal. Pail
Regular price $305.00Regular priceUnit price / per -
Alpha 116113-0005, 857 Water-Soluble Organic Acid Soldering Flux - 5 Gal Pail
Regular price $321.00Regular priceUnit price / per -
Alpha 116016-0005, WS362-25 Halide-Free Water-Soluble Wave Solder Flux - 5 Gal Pail
Regular price $327.00Regular priceUnit price / per -
Alpha 129736-0005, NR330 VOC-Free No-Clean Soldering Flux - 5 Gal Pail
Regular price $246.00Regular priceUnit price / per -
Alpha 152420-0005, EF-8300LR No-Clean Soldering Flux - 5 Gal Pail
Regular price $294.00Regular priceUnit price / per -
Alpha 148691-0005, EF-6100 No-Clean Soldering Flux - 5 gal Pail
Regular price $316.28Regular priceUnit price / per -
Alpha 116400-0005, 926 Scale Remover, 5 gal pail
Regular price $363.00Regular priceUnit price / per -
Alpha 116125-0005, 870-25 Water-Soluble Soldering Flux - 5 gal Pail
Regular price $655.00Regular priceUnit price / per